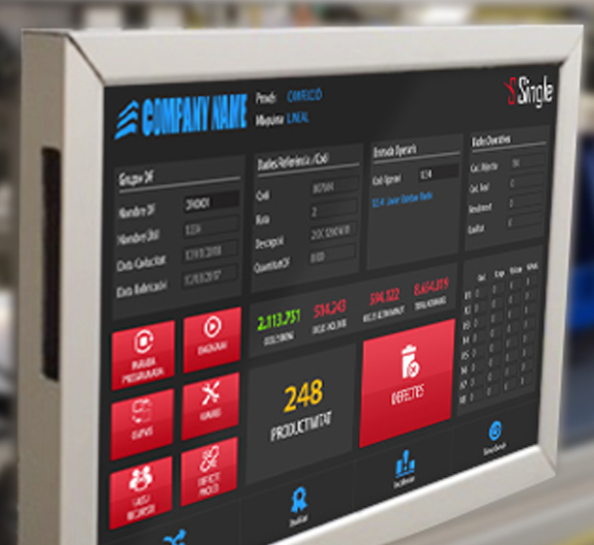
LEAN MANUFACTURING / FACTORY 4.0
"Nuestra misión es preparar a las empresas en la transformación digital mediante un plan formativo de sus empleados ".
En las consultorías Lean Manufacturing diseñamos, formamos e implantamos las bases para la digitalización de la empresa, y durante este periodo instalamos nuestro sistema de captura de datos en planta eKaizen en cada célula piloto.
Áreas de enfoque de consultoría de fabricación.
La Consultoría práctica de Lean Manufacturing orientada a resultados, dirigida a reducir costos, aumentar el rendimiento, reducir los tiempos de entrega y cumplir con las expectativas de los clientes.
- Mejoras de eficiencia: Podemos ayudar a impulsar mejoras en la eficiencia del taller para reducir los tiempos de ciclo, reducir el costo de mano de obra y aumentar la productividad
- Transformación Lean. Eventos Kaizen, control de materiales kanban, 5S, implementación de taller Lean, trabajo estandarizado, mapeo de flujo de valor, efectividad general del equipo (OEE) e inventarios WIP.
- Planificación de capacidad: Podemos establecer métricas y estrategias para ayudar a identificar y superar los cuellos de botella de fabricación y establecer una gestión eficaz de la carga y la capacidad para garantizar que la demanda del cliente se cumpla de manera confiable.
- Métricas y KPIs: Podemos desarrollar y establecer paneles de control, métricas y KPI significativos que estén integrados con sus sistemas para proporcionar una visión clara de su operación.
Los beneficios de Lean Manufacturing.
La implementación de prácticas de Lean Manufacturing en parte significa identificar y eliminar las prácticas y procedimientos derrochadores que son específicos de su negocio, y reemplazarlos con estrategias lean más optimizadas.
- Tiempos de entrega mejorados: a medida que se agilizan los procesos de fabricación, las empresas pueden responder mejor a las fluctuaciones de la demanda y otras variables del mercado, lo que resulta en menos demoras y mejores tiempos de entrega.
- Sostenibilidad: menos desperdicio y mejor adaptabilidad hacen que un negocio esté mejor equipado para prosperar en el futuro.
- Satisfacción de los empleados: los trabajadores saben cuándo su rutina diaria está hinchada o llena de trabajo innecesario, y afecta negativamente la moral. La fabricación ajustada aumenta no solo la productividad, sino también la satisfacción de los empleados.
- Aumento de las ganancias: y, por supuesto, más productividad con menos desperdicio y mejor calidad en última instancia, hace que sea una empresa más rentable.
Capacitación de los empleados
La competencia impulsa la innovación
La digitalización es permitir, mejorar y transformar sus operaciones y procesos de fabricación, aprovechando para ello al máximo las tecnologías digitales y los datos digitalizados. La principal barrera para la implantación de una industria 4.0 es la capacitación de los empleados.
Sin el compromiso de las personas, no es posible garantizar la comunicación digitalizada entre los empleados y las tecnologías de producción digitalizadas.
El conocimiento y la experiencia de los empleados de los lugares de trabajo se pueden utilizar con una alta eficiencia para Aumentar continuamente el rendimiento de los procesos de producción
los principios Lean tienen el potencial para transformar la cultura y el comportamiento de los empleados, a uno que sea más proactivo y eficiente.
Satisfacción laboral
Trabajo bien definido, libertad para realizar tareas, calidad del trabajo y claridad de objetivos.
Implementación Lean
Resultado de la educación, capacitación y participación de empleados que contribuyen al aprendizaje organizacional.
Actividad grupal
Influencia positiva en la satisfacción laboral y la lealtad de los empleados.
Iniciativas de mejora
Lean promueve optimización de recursos, reducción de la variabilidad del proceso y producto libre de defectos que conduzca a mejora en el rendimiento, la calidad del trabajo y la reducción del estrés laboral
BEST PRACTICES - LEAN MANUFACTURING / FACTORY 4.0.
Metodología previa a la implantación de la digitalización en Planta.
Preparación
En esta etapa, se definen los objetivos del proyecto y los recursos.
- Definición de la Visión y Objetivos.
- Definición del equipo de Responsables.
- Planing y definición del Road Map
- Formación inicial al Equipo de Responsables.
Evaluación
En esta etapa, se definen KPI´s, el modelo productivo, y la Zona Piloto.
- Definición de KPI´s para la medición del sistema.
- Generación de Modelo de Gestión de la planta.
- Definición de la célula Piloto
- Definición Organigrama de la zona Piloto.
Implantación
En esta etapa, se realizan la digitalización de la zona, y la certificación del personal.
- Instalación de Equipos de Captura OEE.
- Formación Operarios en Software y OEE.
- Certificación ILUO de operarios.
- Extracción y análisis de Datos OEE.
Control
En esta etapa, se mide y evalúan los resultados.
- Reuniones diarias de Punto Planta.
- Análisis de Eficiencia Planta real vs Objetivo del Modelo.
- Análisis de Métrica de Seguridad, cumplimiento Plan y Stokcs.
- Análsis de Pérdidas de Rendimiento, Calidad y Disponibilidad del Equipo.
Control
En esta etapa, se definen las acciones y Equipos Kaizen.
- Definición de Acciones para aumentar las métricas de la OEE.
- Workshop 5S / SMED / KANBAN / GRUPOS KAIZEN / CHECK LIST / ILUO / STANDARD WORK.....
- Implantación RED BOX para el análisis de Calidad diario.
- Definición de PDCA´s responsables y equipos.
Estandarización / Hábito
En esta etapa, se definien y añade la documentación al Know-how de la empresa.
- Creación y actualizaciónde Estándares.
- Cambios de filosofía "Amor por el Detalle".
- Planning de auditorías para el cumplimiento de Estándares.
- Reuniones de Evaluación de mejoras mensuales por parte de los equipos a la Dirección de Empresa.
Contáctanos!
Pruebas de Software Gratuitas 1 mes.